CASE STUDY
Machine electrical cabinet
We have several customers who use our services alongside their own in-house fabrication and manufacturing divisions. This case study works such a company for food packaging automation; manufacturing machines that pack and seal anything from strawberries to ready meals for leading retailers across the UK.
Precision design, immaculate finishing and swift manufacturing were required for a new electrical cabinet/box for a new automated production machine. We follow it through the factory, from concept to installation.
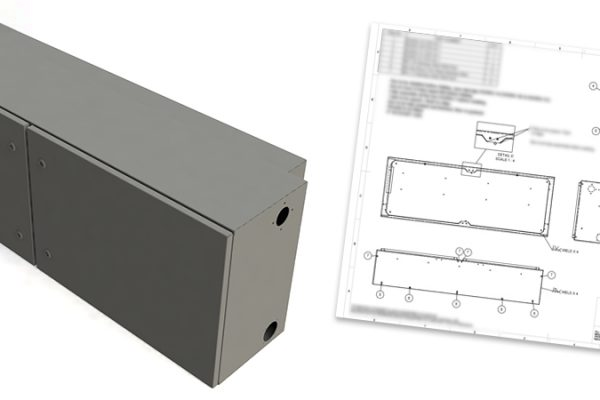
Concept design
Our client already had an existing cabinet design to work from. We were tasked to bring added value to the concept by improving the present construction and utilise modern manufacturing techniques. The electrical metal box is to be constructed from 2mm Stainless Steel, grade 304. With several fixing plates from 2.5mm galvanised steel.
Our CAD engineers can produce exceptionally realistic 3D renders for the customer to get a real sense of reality for the prototype, and end product.
Laser cut
The cabinets flat patterns are laid out in Radan software, and then sent to the laser cutter, along with a few jig patterns to enable effective manufacture by our fabrication team.
Did you know?
You’ll have noticed a film on the sides of the boxes. This is to protect the grained finish of the stainless steel from becoming marked or damaged during production. The film is removed at a further stage.
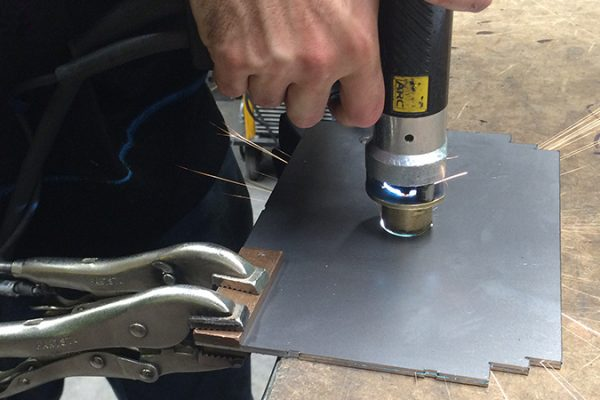
Stud welding
The welder takes all the parts and systematically preps them all. One of the first jobs to undertake is some smaller internal panels and parts that need to have threaded studs welded into place. He places the stainless steel on the workbench, lays a jig over the top (much like a stencil) and then places the stud and welds it into place.
A stud weld is used versus rivets or pemsertted bolts as it doesn’t produce any witness mark on the reverse of the metalwork. It’s more time consuming, but produces a far superior finish for projects such as this.
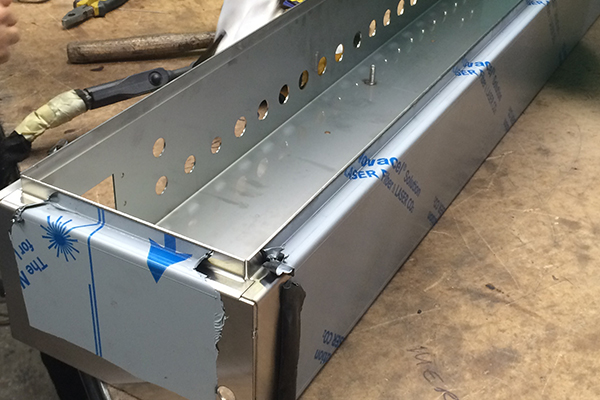
Folds and bends
While parts were being prepped by the welders, the press brake operators folded the main body of the unit that will eventually form the finished box. He then passes the folded parts to the welders, for the next stage of fabrication.
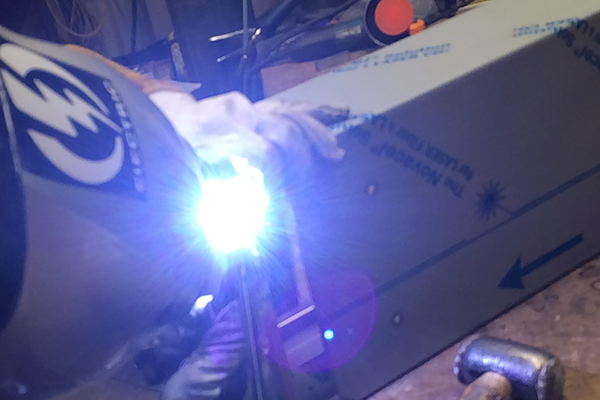
Welding
The tack welds are placed in specific locations, marked out by castellation marks designed into the parts by the CAD team in step one. This gives greater accuracy, a cleaner finish and reduces linishing time.
The cabinet is welded on a clean piece of debris free hardboard so that the machine polished grained sheet isn’t marked whilst the welder manipulates the cabinet into the correct position for performing the welds. After he has tack welded in all the required locations, he begins to TIG weld.
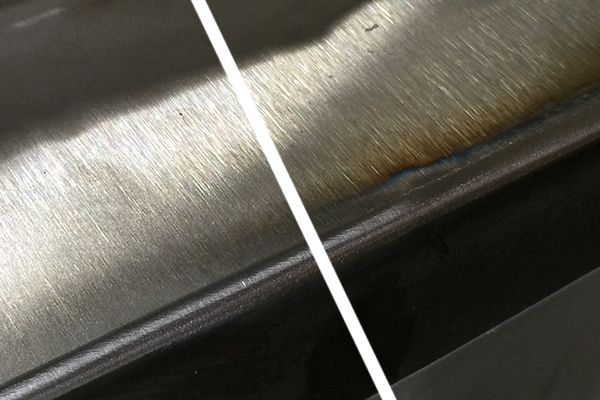
Finishing and Polishing
These electrical cabinets will be supplied in a dull polished or commonly termed grained finish, versus a powder coated finish. This is in part due to the intended purpose being in food production. The grinder starts to grind down all the weld marks and blemishes.
Then he takes a handheld polishing machine and hand finishes the seams so they match the grained stainless steel finish of the rest of the cabinet.
Grinding
Polishing
Construction
The finished electrical box is formed from one large electrical box and one smaller component back box. These are joined together by the bolts stud welded into place in the third stage above.
The electrical boxes are IP65 rated, which means they are Dust proof and Water Jet resistant. This will enable it be cleaned effectively and easily in situ. Therefore a purpose bought in door seal is fitted to create a nice compression seal between the door and the main cabinet. At the same time a top and bottom lock was installed in both doors.
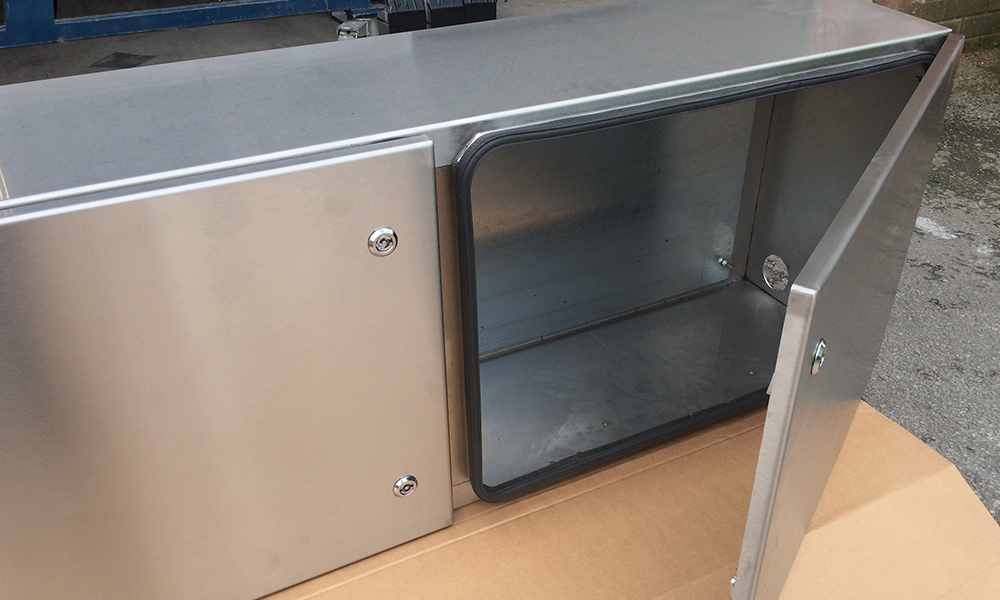
Final product
And here it is! A finished electrical cabinet, for a food production line machine.
We were fortunate that our client sent us a photo of the installed electrical box. We’ve blurred out its internal components for confidentiality reasons.
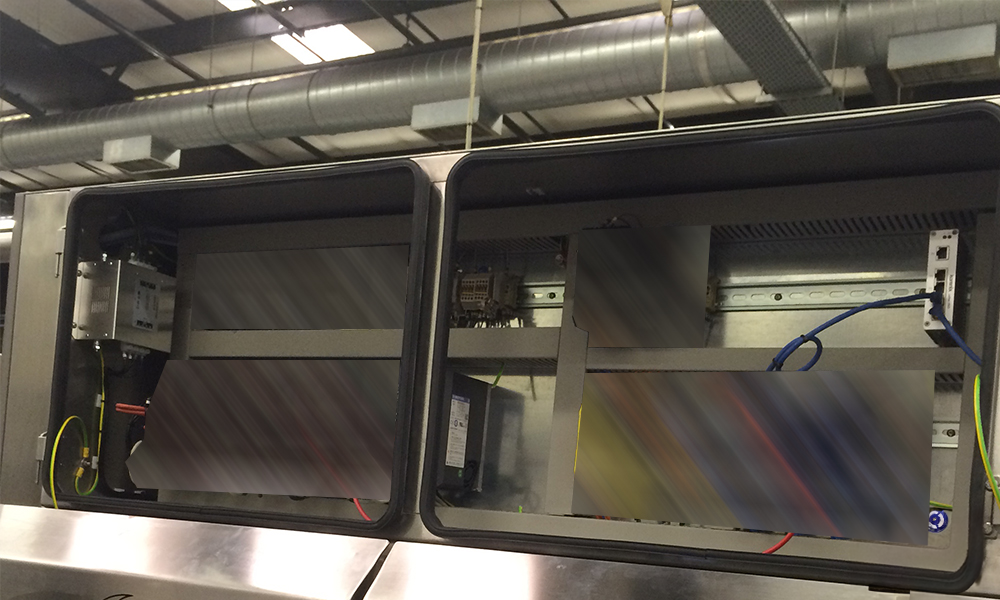
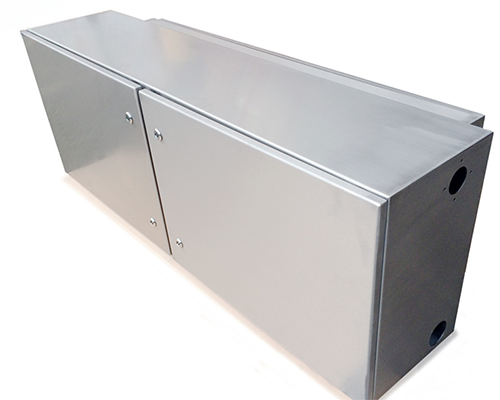