CASE STUDY
Metal food production funnel
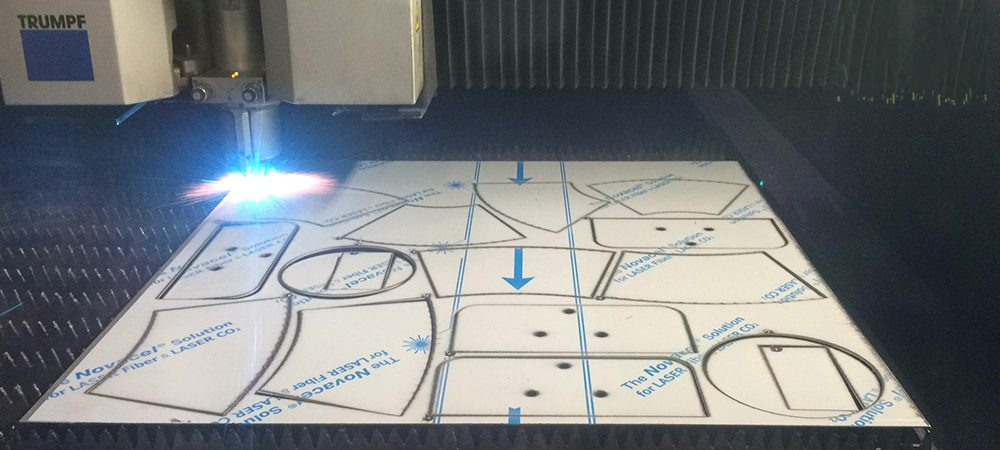
Laser cutting
We start following this case study when it’s reached the laser cutter. It went through the same steps as all our projects, by starting with a consultation with the client and drawing up CAD designs and renders for approval before producing the final product in the factory.
The laser cutter makes quick work of the 2 mm steel the funnel is being manufactured from.
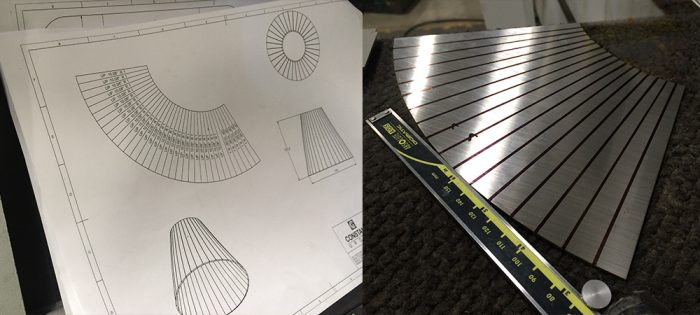
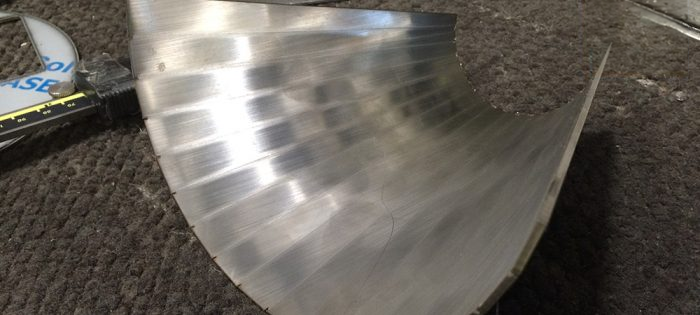
Precision bending
Once cut, the parts are straight to the press brake operators. They take each part and mark carefully the lines for each bend, alongside programming the machines to bend each gradient in succession.
Once the calculations are done, it’s time for the magic to happen! The main funnel is bent in sections.
Welding
And then constructed by the welders into the completed funnel shape with simple tack welds to hold all the parts in place.
Once tack welded into shape, it’s onto the main welding. This funnel involved precision TIG welding to make sure it had the professional and clean finish required for the customer.
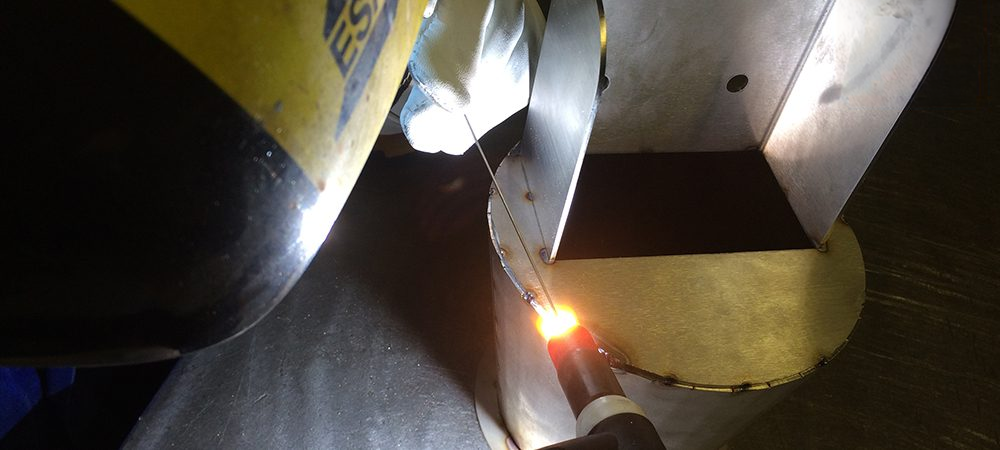
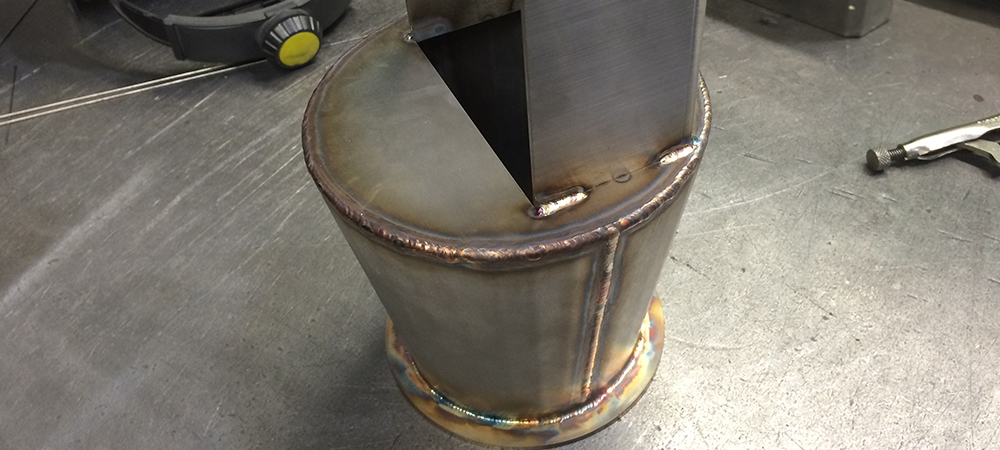
Electrifying finishing
Once the funnel was welded, you can see it had a bit of work required to remove the blemishes and spruce it up to a polished finish.
That means it was time for the grinding, linishing and polishing team to do their magic, but this time there isn’t a grinder or sander in sight.
The funnel is earthed as we apply our special solution which literally burns off the welding marks and reduces all signs of welding on the finished product.
Final product
The funnels were then quality inspected by the QA team and packed off to the customer in Cheshire. This project involved a lot of team work and co-ordination of high-skills from the programming by the CAD design team through to the experienced grinders to polish off and allow the unit to look excellent in it’s natural finish.
