CASE STUDY
Modular retail POP kiosk
We work closely with a range of point of sale and point of purchase clients to help bring new units to market, or simply re-engineer a unit so it’s more cost effective or better to manufacture. One of our clients came to us to work with them on making a traditional table top point of purchase (POP) unit modular so it could be freestanding, as well as be fixed onto a table top.
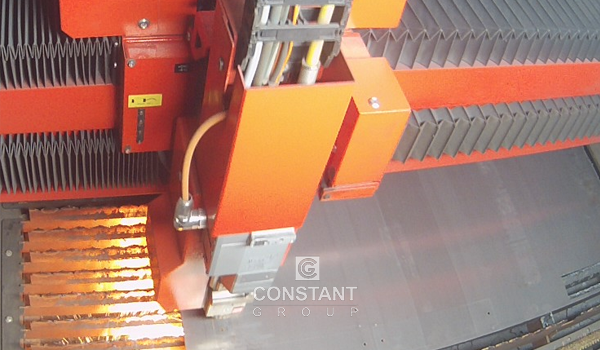
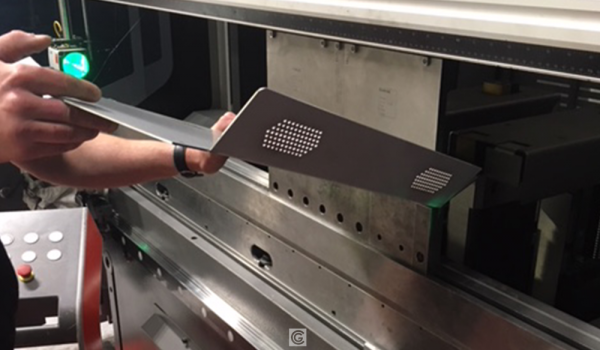
CAD design
The POP unit was to incorporate a chip and pin machine and receipt dispenser so customers can select the product they want from the touch screen display, pay and go to collection.
Considerations had to be taken on the angles of the screen, weight of the unit and where cabling was to be within the unit, all so it doesn’t topple over when fixed to a counter or to a base.
Punch and laser cut
The kiosk unit was manufactured from Zintec sheet metal and started off on our Bystronic fibre laser cutter. The laser made short work of the program designed by our CAD team. The CAD team can watch a visualisation of any project on the laser and press brakes to check it will cut efficiently as well as making sure the program works.
Press brake
Once cut on the laser, the parts were taken to the new press brakes. Each one bent using state-of-the-art precision programming and operator skills. The team check the angles are correct with standard engineering tools such as set-squares and combination squares. Sometimes we manufacture a specific template to check bends to. It’s key this stage is correct, as it can affect the welding and fabrication of the unit if the bends are even out a few degrees, adding on production time and costs.
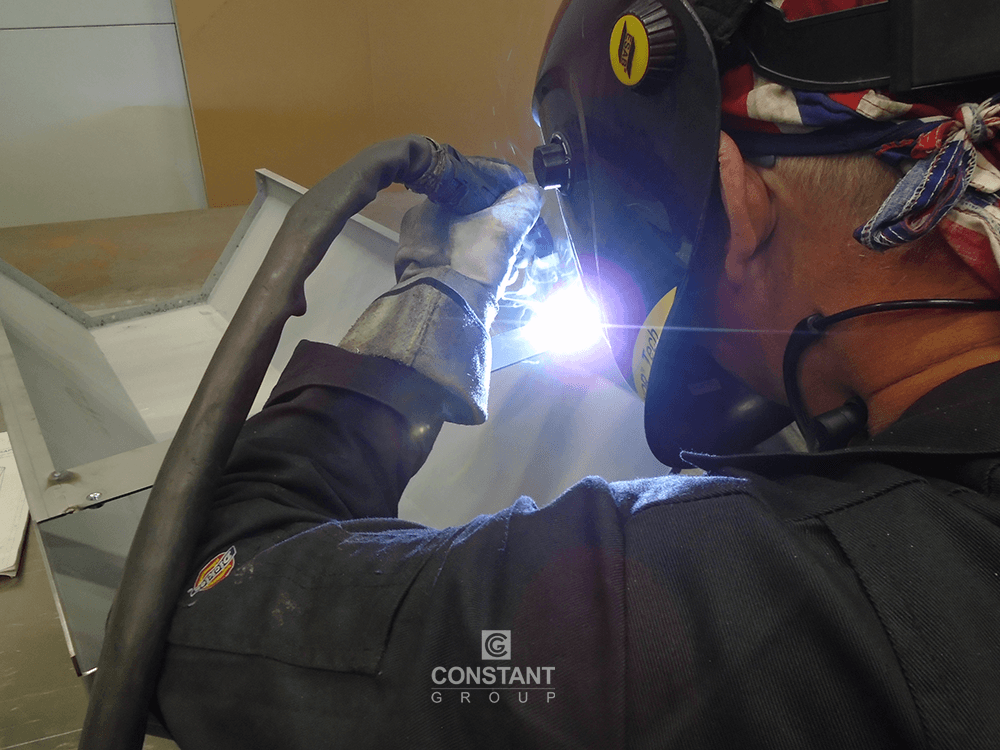
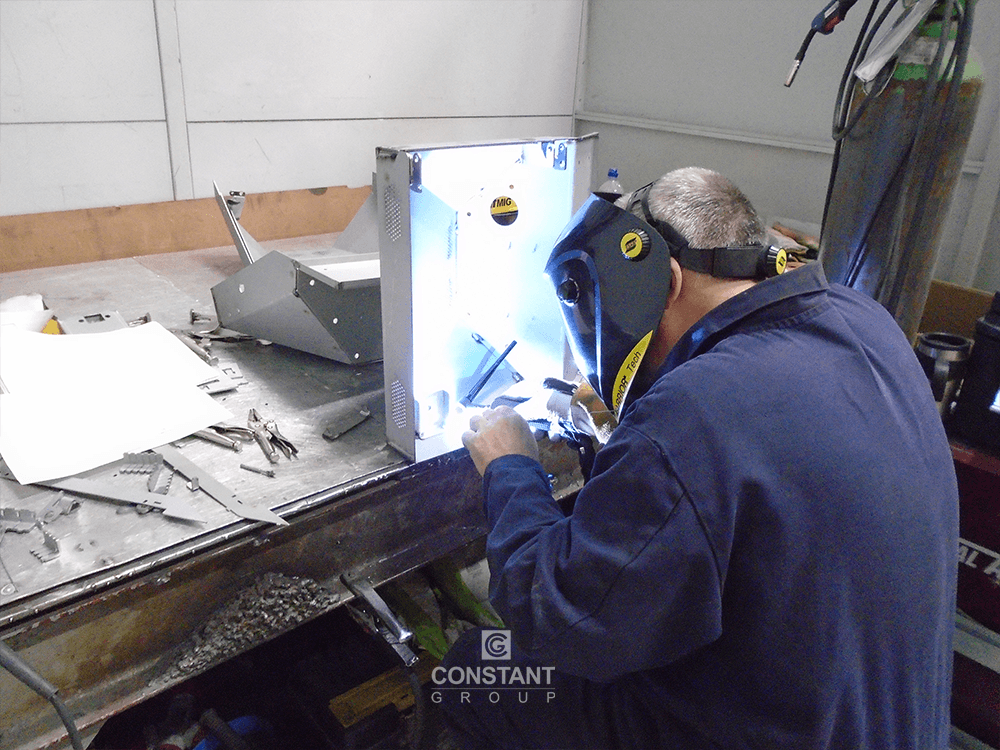
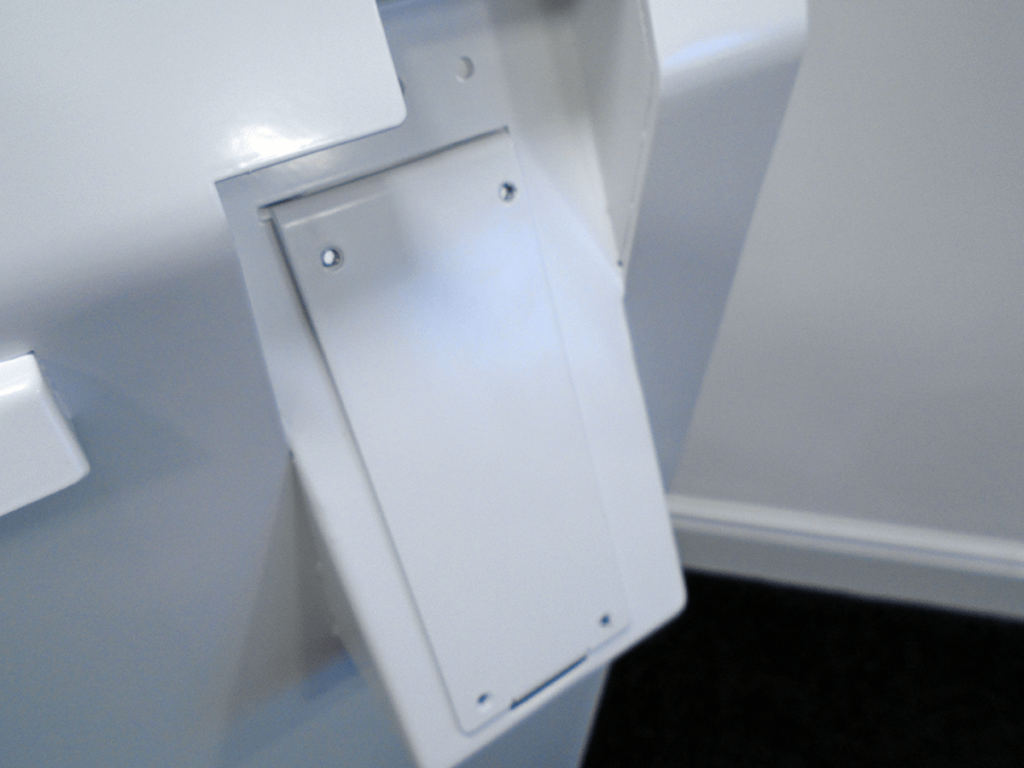
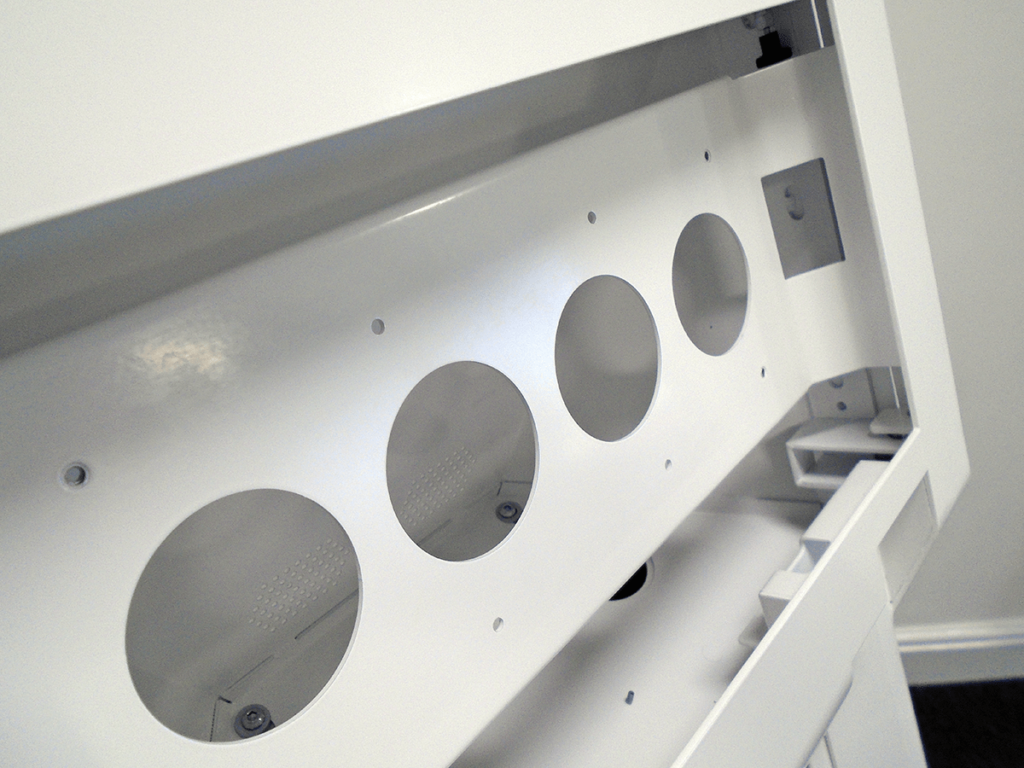
Fabrication
A large and complex metal unit such as this involves a large range of welding, finishing and general fabrication. The welder first aligns all the parts and starts to MIG and TIG weld the unit together. Some parts may be rivetted to speed up fabrication, but only parts that aren’t visible to the public to enable the customer to preserve the unit’s slick white appearance.
Powder coat
Our units don’t go from welders to powder coat plant. First, they are linished and grinded down by our experienced polishing and grinding team. This finishing element of the manufacture reduces any burrs in the metalwork as well as tidying up any welding marks that may be seen in the powder coating phase. The better-quality finish to the metal, the better the powder coat finish will be achieved.
Assembly
With our new factory layout, after our expansion, we have a large assembly area to cope with the increasing demand for full assembly production. These units were assembled by our team, so our client only had to install their equipment and screens. As a result, we installed a blanking plate where the chip/pin/receipt will be housed and made sure a range of options for cabling in the screen and unit were accounted for. These large holes not only give the flexibility for the client to cable efficiently, but they also take some of the weight out of the unit.
Final product
The final product allowed for the top part to be separated from the base pedestal. This gave the client the on-going flexibility to install the units onto a table top, with the front part dropping down over the edge, or installed freestanding in a shopping centre or retail outlet.
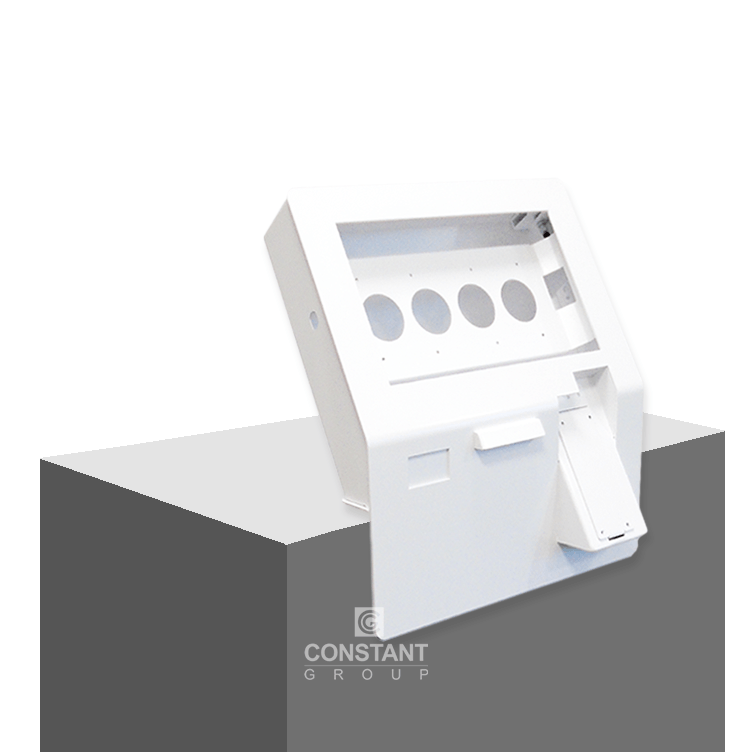
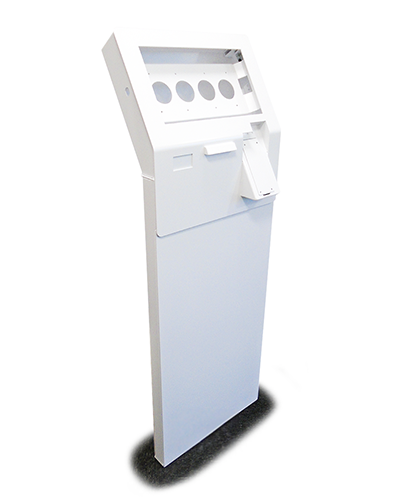